TPEE (thermoplastic polyester elastomer) is a block copolymer containing polyester hard segment and polyether soft segment. Among them, the polyether soft segment and the uncrystallized polyester form an amorphous phase. The polyester hard segment partially crystallizes to form a crystalline micro-region, which acts as a physical cross-linking point. TPEE has the elasticity of rubber and the strength of engineering plastics; the soft segment gives it elasticity, making it like rubber; the hard segment gives it processing properties, making it like plastic; compared with rubber, it has better processing properties and longer service life; compared with engineering plastics, it also has the characteristics of high strength, but better flexibility and dynamic mechanical properties.
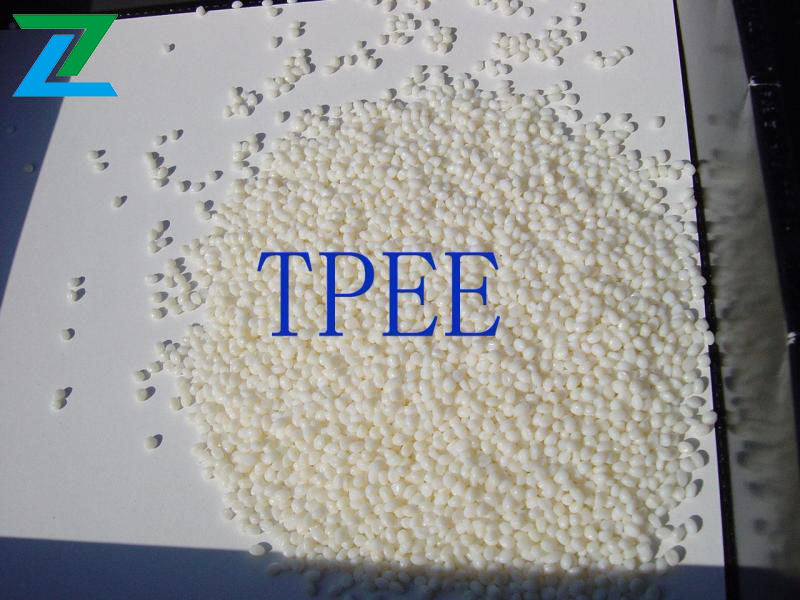
Basic information
Name
TPEE (thermoplastic polyester elastomer)
Mechanical properties
By adjusting the ratio of soft and hard segments, the hardness of TPEE can be from Shore 30-82D, and its elasticity and strength are between rubber and plastic. Compared with other thermoplastic elastomers, under low strain conditions, the modulus of TPEE is higher than that of other thermoplastic elastomers of the same hardness. When modulus is an important design condition, TPEE can reduce the cross-sectional area of the product and reduce the amount of material used. TPEE has extremely high tensile strength. Compared with polyurethane (TPU), TPEE has much higher compression modulus and tensile modulus. When using TPEE and TPU of the same hardness to make the same part, the former can withstand greater loads. Above room temperature, TPEE has a very high bending modulus, but at low temperatures it is not as hard as TPU, so it is suitable for making cantilever beams or torque-type parts, especially for making high-temperature parts. TPEE has good low-temperature flexibility, and its low-temperature notched impact strength is better than other TPEs, and its wear resistance is comparable to that of TPU. Under low strain conditions, TPEE has excellent fatigue resistance and less hysteresis loss. This feature combined with high elasticity makes this material an ideal material for multiple cyclic load use conditions, and can be used for gears, rubber rollers, flexible couplings, and belts.
Thermal properties
TPEE has excellent heat resistance. The higher the hardness, the better the heat resistance. TPEE has almost no weight loss when heated continuously at 110-140℃ for 10h. When heated at 160℃ and 180℃ for 10h respectively, the weight loss is only 0.05% and 0.1%. Therefore, the use temperature of TPEE is very high, and the short-term use temperature is even higher. It can adapt to the paint baking temperature (150-160℃) on the automobile production line, and it has little loss of mechanical properties at high and low temperatures. When TPEE is used above 120℃, its tensile strength is much higher than that of TPU. In addition, TPEE also has excellent low temperature resistance. The brittle point of TPEE is lower than -70℃. The lower the hardness, the better the cold resistance. Most TPEE can be used for a long time at -40℃. Due to the balanced performance of TPEE at high and low temperatures, its operating temperature range is very wide and can be used at -70-200℃.
Chemical resistance
TPEE has excellent oil resistance and can resist most polar liquid chemical media (such as acids, alkalis, and amine diol compounds) at room temperature, but it is powerless against halogenated hydrocarbons (except Freon) and phenols. Its chemical resistance increases with the increase of its hardness. TPEE has good anti-swelling and anti-permeation properties for most organic solvents, fuels, and gases. Its fuel permeability is only 1/3 to 1/300 of that of oil-resistant rubbers such as chloroprene rubber, chlorosulfonated polyethylene, and nitrile rubber. However, TPEE has poor hot water resistance. Adding polycarbonimide stabilizer can significantly improve its hydrolysis resistance.
Aging resistance
TPEE has excellent chemical stability under many different conditions, such as water mist, ozone, outdoor atmospheric aging, etc. Like most elastomers, it will degrade under the action of ultraviolet light. Therefore, for outdoor applications or products exposed to sunlight, ultraviolet light protection additives should be added to the formula, including carbon black and various pigments or other shielding materials; in addition, TPEE has different degrees of hydrolysis.
Product Application
TPEE is mainly used in fields that require shock absorption, impact resistance, flex resistance, sealing and elasticity, oil resistance, chemical resistance and sufficient strength. Such as: polymer modification, automotive parts, high and low temperature resistant wire sheaths, hydraulic hoses, shoe materials, transmission belts, rotational molded tires, flexible couplings, silencer gears, elevator slides, chemical equipment pipeline valve parts, corrosion resistant, wear resistant and high and low temperature resistant materials, etc.